飛行機、船、または乗用車のセダンを生産するかどうかにかかわらず、軽量化はすべての運輸・輸送関連の製造メーカーの大きな関心事となっています。Co2排出量を削減するための規制は世界中のこれらすべての産業に影響を及ぼし、エンジニアは軟鋼などの従来の材料を新しく軽量の材料に置き換え、これらの材料を全体設計に確実に統合できるようにするという新しい課題に直面しています。軽量化によって車両の安全性と信頼性が損なわれることはなく、それを改善する可能性すらあります。材料の選択は、高強度鋼やアルミニウムから、竹やケナフ(インドの麻)のような植物由来の有機繊維までさまざまです。これらの材料が応力下でどのように反応するか、そして異なる材料からなる2つの部分がどのように結合され得るかを理解することは、工学よりもむしろ「錬金術」として説明されてきました。より重い部品を軽量の材料で置き換えることは単なる代用品ではなく、軽量化は設計から寿命まで、製品のライフサイクル全体に影響を与えます。
代替は完璧な世界ではありません
理想的な状況下では、サプライチェーンのすべての製造業者は、軽量の材料として、部品として、または完全な自動車として、最善かつ最軽量の製品を市場に投入するために競争しています。現実には、自動車メーカーがどのモデルに質量削減を適用できるかは、コストによって決まります。カーボンファイバーは軽量化に欠かせない素材ですが、Lucintelの発表によると、下のスライドでは、2025年に製造される軽自動車の5%のみがカーボンファイバーを広く使用し、95%は高コストによりカーボンファイバーをほとんど、あるいはまったく使用しないだろうといいます。コスト削減は大きな影響を与えますが、軽量化はコスト削減に影響を与えうる要素です。LamborghinisとAudi R8には豊富なカーボンファイバーが含まれていますが、ToyotaのYaris(日本名:ヴィッツ)の設計者は現在の価格下で他のより手頃な価格のカーボンファイバーの代替品を検討する必要があります。
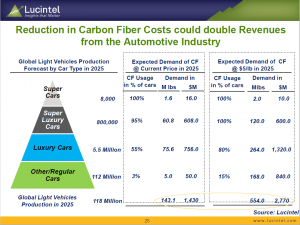
成長する電気自動車(EV)市場がエンジン内燃自動車を衰退させないのかと疑問に思う人もいるかもしれませんが、現実には、ガソリンとディーゼルの機関に自動車がこれから10年の間はまだ存在するでしょう。EVメーカーもまた軽量化に取り組んでおり、バッテリーの重量を減らす方法に焦点を当てています。これは、EVであろうとハイブリッドであろうと、バッテリ―の重量は車両全体の質量に大きく影響しています。
もう一つの制約は材料をリサイクルする能力です。循環経済の台頭はこれを必要とし、それに従わない生産者は罰せられる可能性があります。そのため、費用対効果の高い材料を発見し、使用環境に近いストレス下で長期間にわたってその適合性をテストし、現在のモデルで使用されている材料の代わりにそれらを利用することが企業間の競争のスタートです。
コンセプトとデザイン
特定の材料の選択は設計プロセスに劇的な影響を及ぼします。それがうまく使用されることができると判明させるために採用前に、徹底的なテストがされなければなりません、そのほとんどはシミュレーションソフトウェアを使用し、材料とプロトタイプの実際のテストを補足するでしょう。シミュレーションアプリケーションのプロバイダは、新しいシミュレーションツールをシミュレーションツールキットに追加する必要があることを認識しています。シミュレーションソフトウェアのリーダーであるAltairは、最近Cambridge CollaborativeのSEAM® ソフトウェアを買収しました。このソフトウェアは、大手企業によって、特に車内の振動や騒音の可能性をテストするために使用されてきました。
Autodesk Universityは、短繊維と連続繊維のテストが異なる、繊維を含む熱可塑性複合材料をテストするためにどのようなシミュレーションが必要かにおいてトレーニングがあります。
材料の試験は、その材料が新しい設計に使用されることが決定された後にも中断されることはありません。エンジニアは、現場の材料や部品を監視するためのセンサーを含めています。このセンサーからのリアルタイムデータは、製品の耐用年数の間に製造元に加えて、通常はその一部のデジタルツインまたは車両全体にまで伝播されます。仮想バージョンでおけるあらゆる欠点を特定でき、是正措置または改善を次のモデルに適用できます。Ansysは、シミュレーションのリーダーでもありますが、最近、デジタルツインソリューションをサポートするために彼らのTeamworx IoT プラットフォームでPTCと提携しました。
エンジニアリングのもう1つの新しい分野は、異なる材料を接合するための新しい方式と、従来のナットとボルトが不適切なケースにおける接合のための新しいファスナーの発見と設計です。結合部分にファスナーを使用すによって振動や騒音も減少します。最近の研究は可逆的な熱可塑性樹脂用の結合剤を開発しました。ボンドを形成するために熱が加えられ、必要なとき、例えば使用中に、ボンドを除去するためにボンド素材が再加熱されます。部品を再接着するには、再度熱を加えます。ミシガン大学の研究者達はこのイノベーションのためにナノテクノロジーを使用しました。
組立ラインの再考
組立ラインの伝統的な線形プロセスは陳腐化する可能性があります。BMWは、より柔軟で機動的な新しいパラダイムに移行しています。パワートレインごとに異なる組立ラインを用意するのではなく、製造現場を再検討したため、共通の組立ラインを介してエンジン車、ハイブリッド車、または完全電気自動車を生産することができます。これにより、カスタマイズを新しいレベルに引き上げることができます。アウディも製造現場の将来の傾向に対応するために製造現場を再設計しました。
予防的メンテナンス
デジタルツインの使用により、積極的なメンテナンス、差し迫った欠陥と損耗が車に埋め込まれたさまざまなセンサーによって監視され、ディーラーや会社に報告されます。結果として、車両の所有者は自分の車をメンテナンスや修理のために持ち込むように促される可能性があります。これはテスラですでに実際に起こっています。テスラで生産された各自動車はそれ自身のデジタルツインを持っており。ソフトウェアダウンロードは所有者が心配のために自動車を持って来なければならないケースよりもどんな問題に対しても一番の優先事項です。自動車の修理やメンテナンスに関しては、従業員は使用される新しい材料、および非接着部分をリバーシブルボンドで接合するなどの技術についてのトレーニングが必要になります。これは可能な限り自動化される可能性が高いですが、プロセスと材料を十分理解している従業員は依然として必要とされるでしょう。
ラインの終わり
寿命が尽きて自動車がスクラップヒープに追いやられる日々は終わりを告げました。部品は地球への負荷を減らすためにリサイクル可能である必要があります。コンセプトとデザインを考慮しつつ適切な材料を選択することが重要です。部品は車両の耐用期間において耐久性があり堅牢である必要がありますが、それらはまた容易に再生可能であることが求められます。これが達成されるために消費されるエネルギーは、非常に低いか、または使用される材料の固有の品質によって相殺されるべきです。インド麻やケナフは、適切な材料の一例であり、それは大気中から二酸化炭素を抽出する能力と4ヵ月の急速な成長サイクルによってカーボンニュートラルです。 マレーシアは、軽量化の製造においてケナフの市場が間違いなく活況となることを見越して、成長するケナフ市場に大きな投資をしました。
新しい複合材料とそれらの特性を理解することに関する推測と研究は、研究を行う専門組織によって効率化されました。研究大手のFraunhoferは、デジタルツインの素材を開発しました。これは、製造者がアクセス可能な素材データベースに格納され、当面の問題に最も適した素材が何かを決定します。意図は付加的なエンジニアリング環境をサポートすることでしたが、それは他の製造上の課題に対しても同じく効果的です。
軽量化の促進は、自動車や飛行機に限らず、家電製品から風力タービンまで、あらゆる製品が、軽量化とローターブレードのリスクの軽減から、現在使用されているものより優れている新しい複合材料まで、いずれからも利益を得ることができます。 センサーのコスト削減は、現場での製品について報告するためのデジタルツインの使用を促進し、継続的な改善サイクルを生み出します。